
The Comfy Crutch
Problem and Background
A torn ACL is one of the most common and devastating injuries for college athletes. Although reconstructing an ACL is a relatively routine procedure, patients need up to fourteen months to fully recover post-surgery.
​
The first few weeks following surgery are when the patient is most sensitive to pain and needs to be extremely careful to not re-rupture the graft. Patients use crutches for up to six weeks following the surgery, and in between brief periods of hobbling around, RICE (rest, ice, compression, and elevation) is critical.
​
Unfortunately, finding an adequate place to rest and elevate one's leg isn't as easy as it sounds. College students who have torn their ACLs report that even if they are lucky enough to find an unoccupied chair, resting the injured leg on a chair is uncomfortable for the duration of class. Others give up entirely and sit on the floor. Shocked that there were so few accommodations in classrooms for people with this relatively common injury, my group sought to create a solution.
The Process
Observations and Research
First, we interviewed potential users, and conducted research on the current state of the art of crutches and footrests.



Next, we complied our research into a list of specifications that our device had to meet. We then created this matrix, which ranks the specifications (top 3 are boxed), justifies why each is necessary, and explains how to quantify and test them.

Prototypes
We created numerous prototypes, each of which honed in on one specification or aspect of the device.
This strategy allowed for rapid iteration and testing without having to make multiple high-end prototypes.




Spring-loaded Catch
A spring-loaded groove held this wooden plank in place, which could swing down and provide support when the crutch was in legrest mode.
3D Printed T-Connector
The main body of the crutch was sawed in half, and could be reconnected with this piece to form either a 90 degree angle for legrest mode (shown here)Â or 180 degrees for walking support.
Swinging Axis
We took advantage of the crutch's design by rotating the main column 90 degrees to switch between walking and legrest mode.
Double Support Bar
This wooden rectangle was able to hinge between being flush against the crutch body for walking, and perpendicular to the crutch body for legerst mode.
Testing
To compare the various prototypes, we tested them to see how well they each satisfied our specifications.
We refined the designs that performed the best, and eventually amalgamated them into a final device.
Final Prototype and Key Features
.jpg)
Walking mode
Here's the crutch when all of its components are folded up, flush against the original crutch frame. We wanted it to be sleek, elegant, and lightweight as to not interfere while the patient is walking.
.jpg)
Leg Rest Mode
This is what the crutch looks like when all of its components are fully deployed for it to be used as a leg rest.

Bottom Support
We modified the original crutch so that this bottom piece, which uses button clips to make the height of the crutch adjustable, can pivot to become perpendicular to the body of the crutch.

Bottom support locking mechanism
We used a bike skewer (what you use to hold your bike seat at the desired height) to lock the bottom support piece in place after pivoting it ninety degrees.

"H" Support
Similarly to the bottom support piece, this H-shaped piece of metal unfolds until it is perpendicular to the frame, and is also held in place with bike skewers.
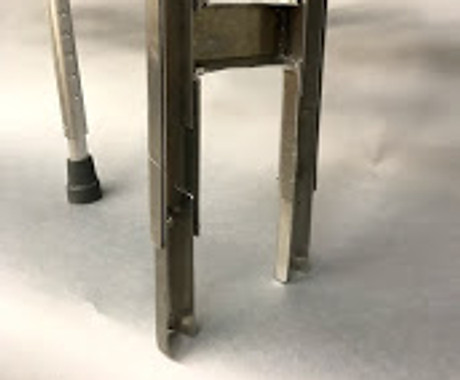
"H" Support Height Adjustment
The two long sides of the H have a smaller piece of metal inside, which can be slid up and down within the larger frame to adjust their height in conjunction with the length of the bottom support piece.
Takeaways
What I Learned
I took the lead on fabricating our prototypes, so I spent a significant amount of time in the machine shop for this project. The tools I worked with and skills I learned include, but are not limited to: mill, lathe, bandsaw, sander, sheet metal bender, hand drill, and hand saw.
​
Outside of the machine shop, this project honed my teamwork, brainstorming, listening, and presentation skills.
Next Steps
Many of the people we talked to who had suffered through a torn ACL were ecstatic about our idea and said that it would have greatly improved their quality of life during the first few weeks post-surgery.
​
Based on user testing with the device, some of the things we can improve upon in future designs are stability and the height adjustment of the "H" Support.
​
Below are my team members for the project and our primary roles. We had an awesome time working together, and are considering moving forward with a patent for our invention.
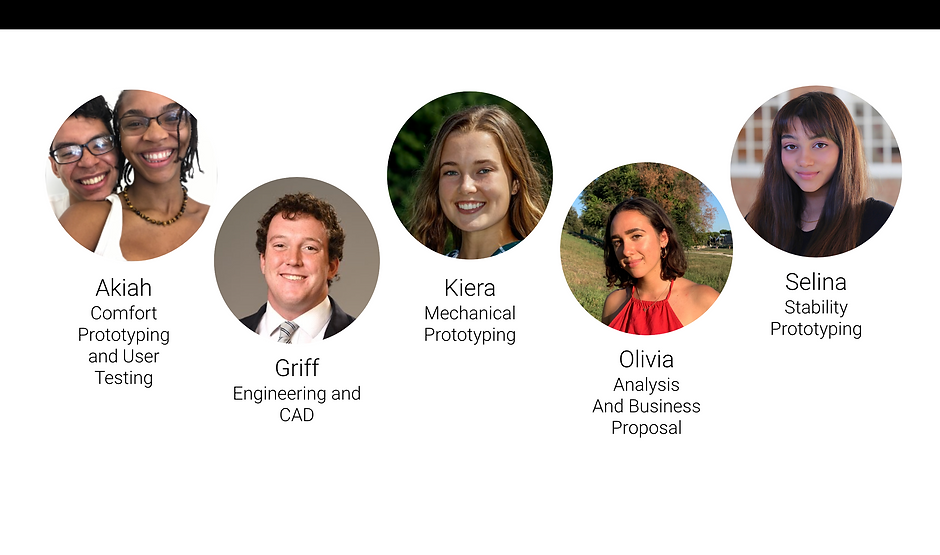